Senior thesis presentations (Academic Year 2024)
On March 12, 2025, Mr. Yuma Inaba, Mr. Hirofumi Imamoto, and Mr. Yusuke Kitano, fourth-year undergraduate students in the Umedachi Lab., presented their one-year research results at the senior thesis presentation of the Functional Mechanics Course, Department of Mechanics and Robotics, Faculty of Textile Science and Technology, Shinshu University. Their outcomes will be presented at the Japan Society of Mechanical Engineers Conference on Robotics and Mechatronics 2025 (Robomech2025, Japanese conf.). We plan to bring a demonstration machine, so please drop by if you are attending the conference.
Snake-like robot that crawls diagonally sideways by both bending and telescopic motion
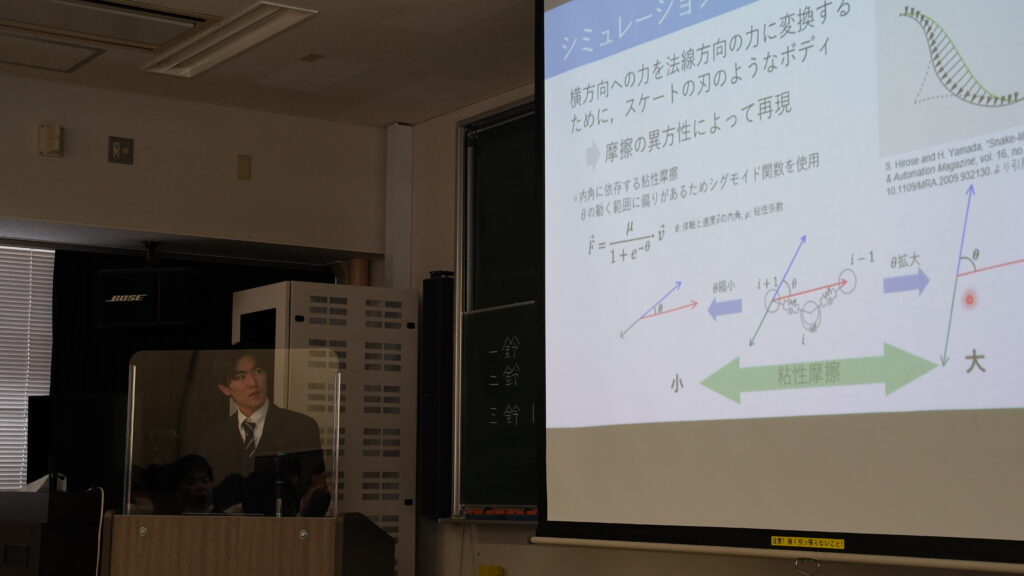
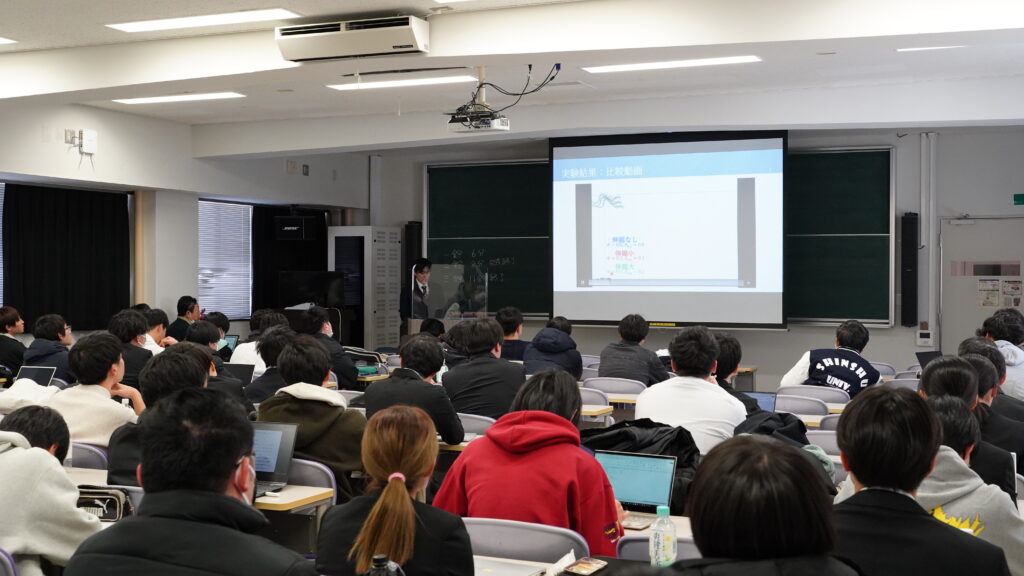
Presenter: Mr. Yuma Inaba
Mr. Inaba developed a snake-like robot with a new movement style by introducing telescopic motion in addition to the conventional bending motion. He analyzed the motion characteristics using simulations and confirmed that the snake-like robot could move in an oblique lateral direction by controlling the amplitude and phase difference of the telescopic motion. Based on the simulation results, he is designing a prototype robot. The results of this research are expected to lead to the development of robots with flexible adaptability to the environment by proposing a new mobility strategy for biomimetic robotics.
Autonomous skeleton design of soft robotic hand that adapts to shape of a grasped object
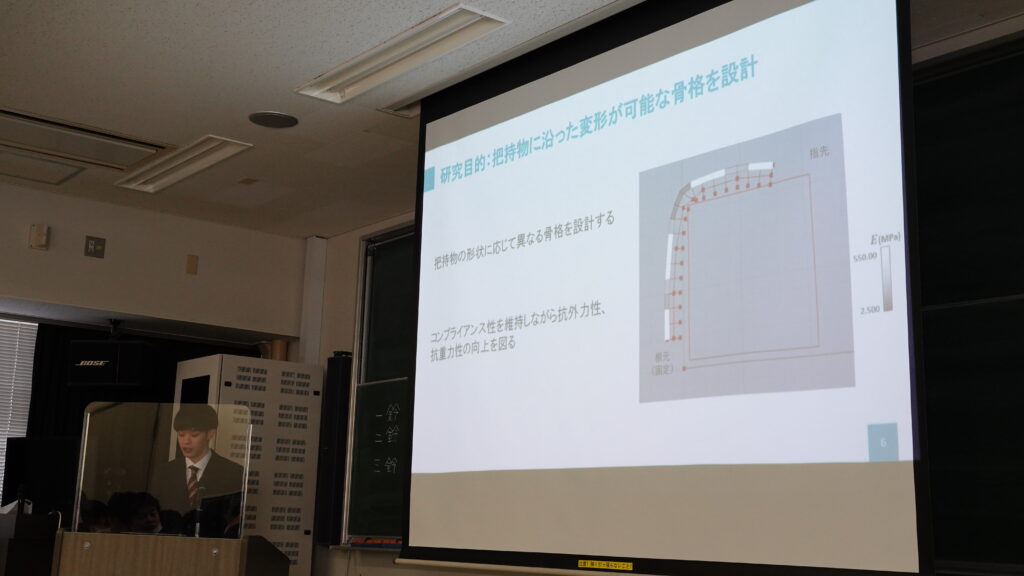
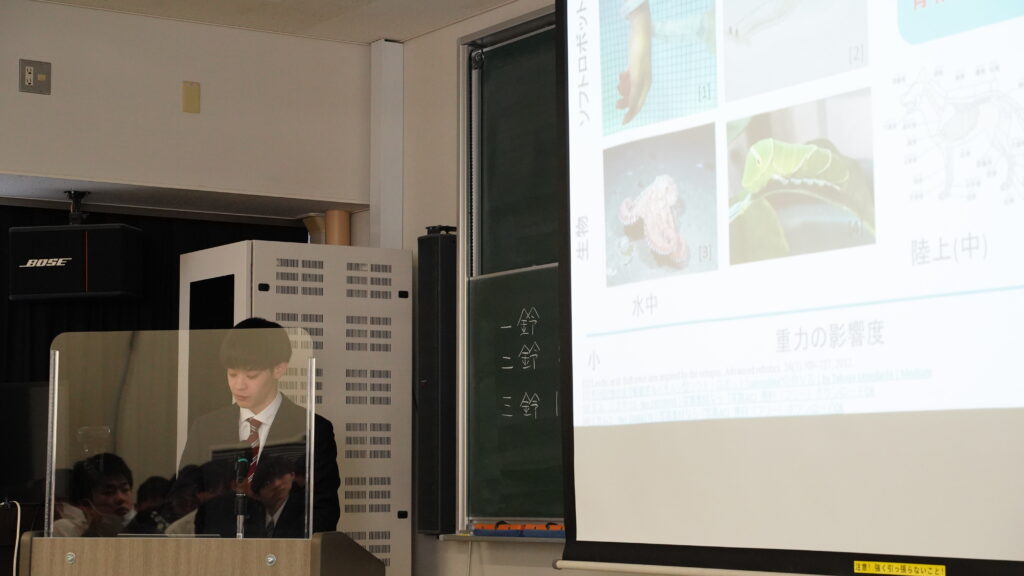
Presenter: Mr. Hirofumi Imamoto
Mr. Imamoto designed an autonomous skeleton design algorithm for a soft robotic hand based on the shape of the object to be grasped, using the reaction-diffusion equation used to generate the skeleton in living organisms. While soft robots are highly adaptable to the external environment due to their flexibility, they lack an appropriate support structure when grasping heavy objects. In this study, he designed a skeleton that adapts to the shape of the grasped object and deforms to improve its anti-gravity and anti-external force properties while maintaining compliance. Through simulations, it was confirmed that the skeleton is generated in accordance with the shape of the grasped object through physical interaction with the grasped object of different sizes.
Development of 3d-printable and tunable tensile-stiffness element
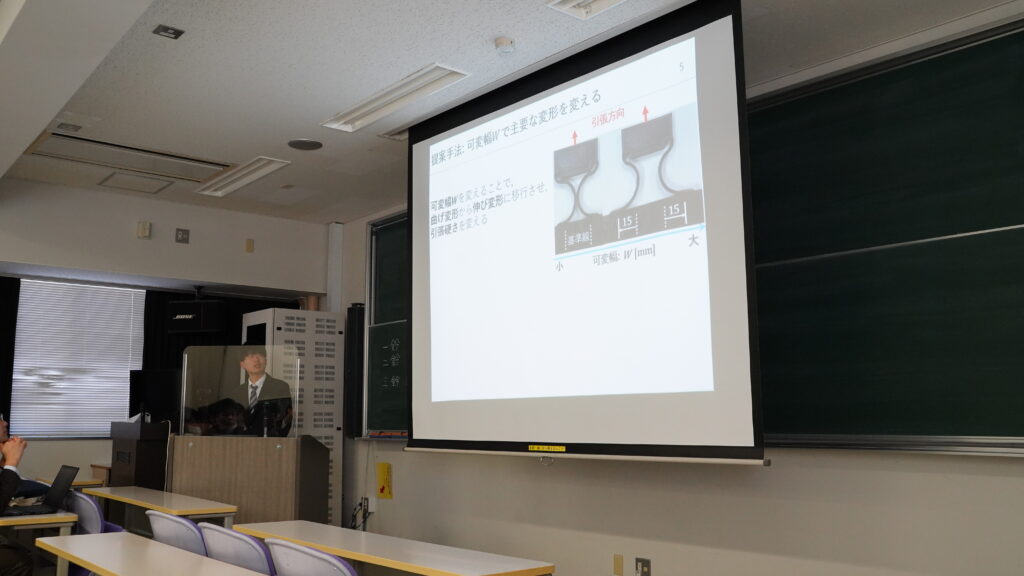
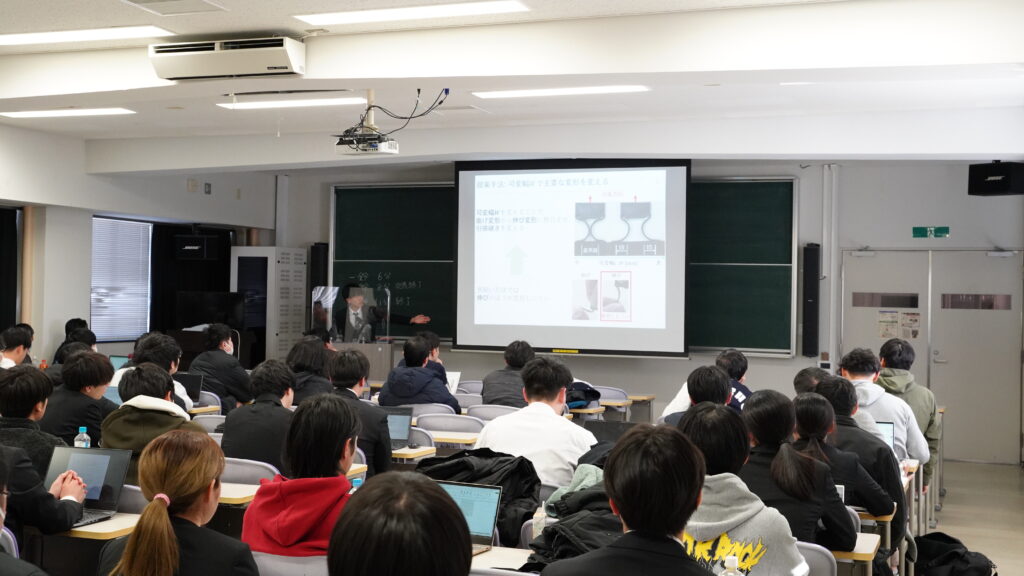
Presenter: Mr. Yusuke Kitano
Mr. Kitano developed a mechanism to shift the main deformation mode of the structure from bending deformation to elongation deformation by manipulating the variable width W. Using TPU (thermoplastic polyurethane) as the material. He developed a tensile-stiffness tunable element that can be fabricated using a 3D printer. Through experiments and simulations, he has confirmed that this method enables the tuning of tensile stiffness. The results of this research are expected to be applied to soft robotics to improve the flexibility of robots and as a new design guideline for compliant mechanisms. In the future, we plan to develop a more miniature robot and introduce a motorized control mechanism, aiming for practical application.